7 Ways to Improve the Energy Efficiency of Solar Well Pumps
- Share
- Issue Time
- May 11,2022
Summary
Energy efficiency is an important topic with increasing concerns about the environment and the need to reduce costs. This article describes 7 ways you can save energy on your pumping system.
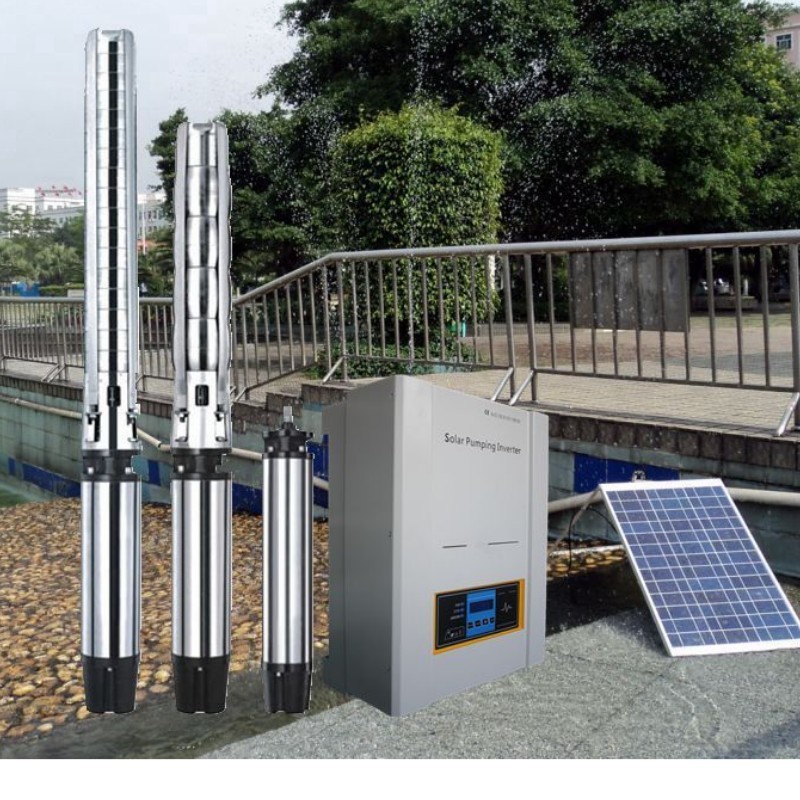
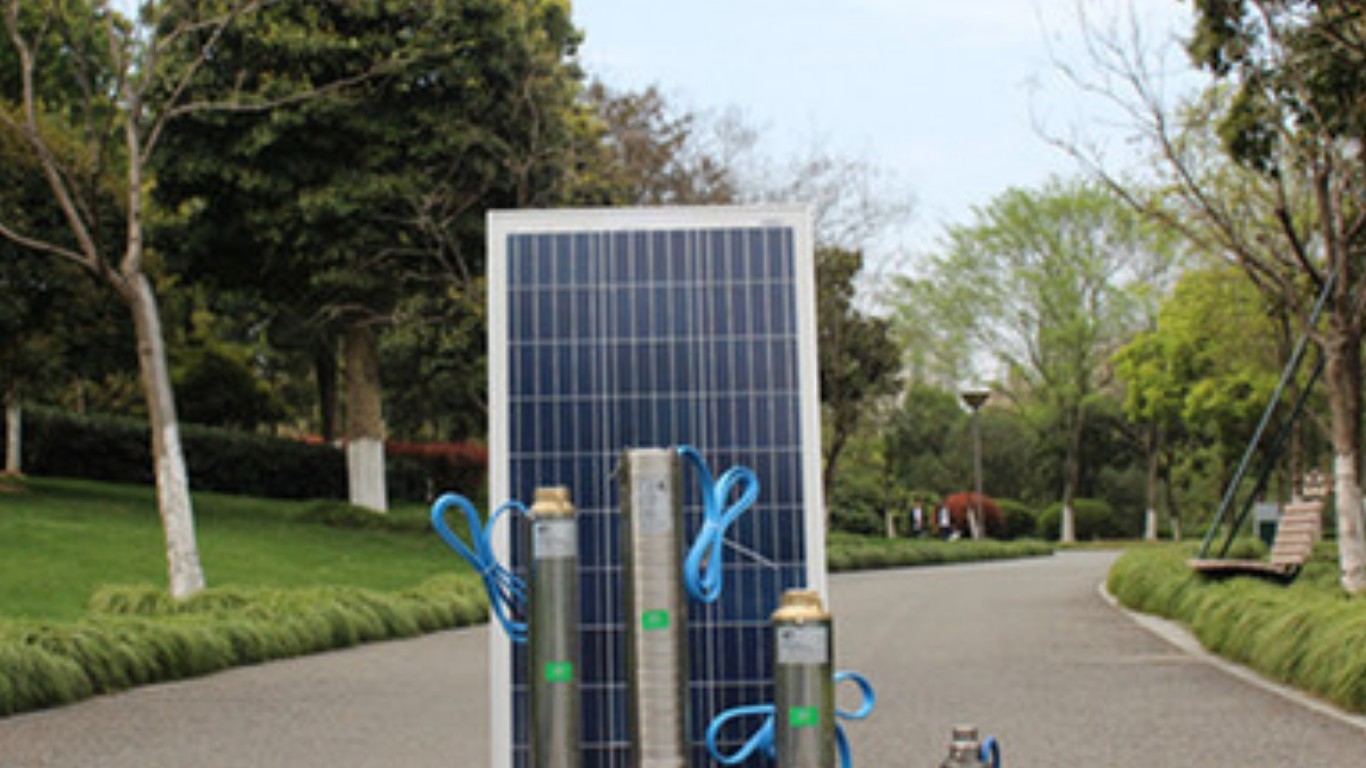
Energy efficiency is an important topic for the industry with increasing concerns about the environment and the increasing need to reduce costs. Pumped water systems reportedly account for nearly 20 percent of the world’s electrical energy needs, and U.S. Department of Energy study found that 16 percent of the electricity cost of a typical industrial facility is generated by its pumping system. This alone shows how important it is to improve the energy efficiency of pumping systems...
This article describes 7 ways you can save energy on your pumping system.
1. Avoid oversized pumps
Engineers are often conservative when specifying solar well pumps, and they usually include a margin of safety in the duties of the supplied solar well pump compared to application requirements. It is well documented that rotodynamic pumps such as centrifugal pumps make up around 80% of all installed pumps and are often 20-30% oversized. Oversized solar pumps can lead to unnecessary energy consumption as higher performance in flow and pressure requires more power from the motor.
While some degree of oversizing may be good common sense to compensate for uncertainties in the design process, choosing a pump that operates as close to its optimum efficiency point as possible can significantly reduce energy usage.
2. Impeller trimming
If the solar well pump is oversized, trimming the impeller is a relatively cost-effective way to reduce the pressure and flow produced. While trimming the impeller is more energy efficient than using a throttle to achieve the required work, when the impeller is shaved, the gap between it and the casing becomes larger, making it less efficient than a full-size impeller. Therefore, variable speed drives are often preferred when it comes to energy efficiency.
3. Variable frequency drive
As the name suggests, variable frequency drives vary the speed of the motor to achieve the actual head and flow needs of the application, not the flow the pump can produce. VFDs are commonly used to limit unnecessary energy consumption in two situations; the first is to reduce motor speed on pumps that are oversized at the specification stage.
The second use of VFDs is to have different operating requirements for the pump at different times. In this case, the pump needs to be able to run at maximum capacity when needed but may run below this capacity for extended periods of time. A typical example is a cooling pump, where the temperature of the equipment/fluid that needs to be cooled can vary widely.
While VSDs do come at a cost, often the energy cost savings they can save justify the investment.
4. Parallel pumping system
For systems with different load requirements, using multiple pumps is an alternative energy-saving solution to VFDs. When "worst-case" conditions are significantly more demanding than normal operating conditions, the majority of the working life of a single well pump may be operating far from its optimum efficiency point. Installing a second, smaller well pump to meet average system demands will relieve the larger pump from operating well below its optimum capacity.
5. Limit pipeline pressure loss
Optimizing system piping to limit frictional pressure drop is another energy-saving method, as it reduces the power required by the solar well pump to overcome such losses. Pipe diameter, length, interior surfaces of the layout, and components installed within the pipe all affect system pressure drop, so these factors should be considered when considering energy improvements.
During the design phase, the number of bends, expansions, and contractions in the pipe should be minimized, keeping the pipe as straight as possible and of the same diameter. However, this is not always possible due to space constraints. Any fittings or valves specified for installation should also have relatively low-pressure drops.
Also, the diameter of the pipe should be chosen carefully, as a smaller diameter will cause more friction. Pipes can be expensive, especially if the fluid being pumped requires more expensive materials (such as stainless steel), so there is often a tendency to make pipes smaller in diameter. Corrosion and rust increase resistance and reduce pressure loss, which means that cleaning and maintenance of pipes are also important.
6. Eliminate unnecessary usage
While this may seem obvious, it is surprising how often the pump runs unnecessarily. A control system can be implemented to shut down pumps that are not in use, such as backup pumps, and when load requirements change, a pressure switch can be used to control the number of pumps in operation. This ensures that multiple pumps are not used at the same time when current system conditions require only one pump to operate.
7.Perform maintenance
Routine maintenance of the pump can also reduce energy consumption, and like any equipment, wear and tear reduce efficiency. Maintenance of the pump including replacing worn wear rings is critical as increased wear ring clearance increases leakage and therefore pump power requirements to produce the same flow. The energy efficiency of the pump may decrease by 10-25% until the pump is replaced. At this stage, the best way to reduce your pump's long-term energy costs is to upgrade it!
The above are ways to improve the efficiency of solar well pumps, if you want to buy solar well pumps, please contact us.
TPON is a professional custom solar water pump manufacturer. All the important parts of the solar water pump are manufactured and processed by our factory. The workshop is equipped with automatic winding machines, finishing equipment, advanced assembly lines, and precision testing machines. Each solar well pump will be rigorously tested before leaving the factory to ensure product quality.